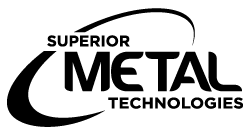
Anodize Overview
Aluminum anodizing is the process of electrochemically changing the thickness of the natural oxide layer on the surface of aluminum metal. As part of the process, some aluminum material is removed or etched away while the top natural oxide layer is built up. Unlike most other finishes, anodized aluminum preserves the natural luster, texture, and beauty of the metal itself. The resulting protective aluminum anodize layer is harder and more durable than almost any other material known to man, second only to the diamond. It's an excellent aluminum finish in high-traffic areas where resistance to wear and tear is required.
- Corrosion Protection – anodized aluminum resists moisture, salt spray, UV radiation
- Durability – long life span, will not wear out under normal use
- Color Stability – electrolytic process provides resistance to UV rays - anodized aluminum won't fade, chip or peel
- Ease of Maintenance – highly resistant to scratches and wear, cleans easily with mild detergent and water
- Aesthetics – offers a large number of gloss and color alternatives
- Cost – lower finishing cost, lower maintenance costs
- Health / Environmental Safety – anodized aluminum produces no dangerous by-products – and anodized aluminum does not harm human health or the environment
Color Options
We focus primarily on standard architectural aluminum anodize color finishes. These include various clear anodize, champaign anodize, bronze anodize, and black anodize. We can help color match within these color tones, but we do not offer gold or other color-dyed anodize options at this time.
While our process allows us to match relatively closely, material thickness, lengths, surface finishes, alloys, perimeters; etc. make a perfect color match between each piece virtually impossible. On-screen and print colors may very from actual anodized materials.
Clear Anodize
201-R1 Class II (0.2mil)202-R1 Class II (0.3mil)
204-R1 Class II (0.5mil)
215-R1 Class I (0.7mil)
Champagne
Anodize
Light Bronze
Anodize
Medium Bronze
Anodize
Dark Bronze
Anodize
Black
Anodize
Standards-Based Process
Our acid etch anodize and caustic etch anodize processes meet Type II Class 1 performance standards. These specifications provide a benchmark for high-quality anodize coatings throughout the aluminum finishing industry. With a minimum mill thickness of 0.7 (18 microns), the material is suitable for coastal climates and provides resistance to corrosion and discoloration.
While our modified hardcoat anodize, does not meet Type III Class 1 standards, it does offer a harder finished product compared to our other anodize processes and has successfully been used in pneumatic tubes and other custom applications.
Step | Description |
---|---|
Cleaning | Removes fabrication oils and buffing compounds by soaking the work in a water-based solution containing mild acids or alkalis along with dispersants and detergents. |
Pretreatment (Optional) | Used primarily for decorative purposes to improve the appearance of the aluminum surface prior to anodizing. The most common pretreatments are: etch, which imparts a satin, matte finish; and bright dip, which imparts a bright, shiny finish. |
Anodizing |
Produces the actual protective oxide coating. Depending on the selected anodize process, the material is submerged in a bath of water and chemicals. A direct electrical current is passed through the material, at which point the water breaks down, liberating oxygen at the surface of the material. This process then combines with the aluminum to form a coating – a transparent and microscopically porous layer of aluminum oxide. Thickness is determined by the level of electrical current and the length of time that current is applied to the material. For quality purposes, the material is tested for coating thickness prior to moving on to the next step in the process. |
Electrolytic Coloring "Two-Step Method" (Optional) | Anodize is traditionally clear by nature, taking on the color properties of the base material. We offer an optional two-step process that can impart color to the coating after it is formed. This process takes advantage of the fact that the freshly anodized coating is porous and therefore capable of absorbing colorants. |
Sealing | The pores on the surface of the finished aluminum parts need to be closed before being placed into service. If left unsealed, the aluminum surfaces could have poor corrosion resistance, or absorb unwanted stains. |
Quality Inspection | As the material is unracked from the line it undergoes a rigorous quality inspection to verify the finish meets all defined specifications and Superior Metal Technologies quality standards. |
Anodize Line Maximums
If you have parts or materials that exceed these maximums, we may be able to accommodate or provide recommendations on how to best process the material. Please make sure to detail any oversized parts, their dimensions, and any other relevant information when you request a quote.
Dimension | Maximum |
---|---|
Length | 32' 6" |
Height | 5' |
Width | 30" |